A wrought iron artist is a “blacksmith (Kajiya in Japanese)”.
In the West, a blacksmith is called “Blacksmith” because “Black” signifies iron and “Smith” signifies a craftsman.
The name “41 FORGE” is the artist Shinichi’s play on words. Shin is “4” and ichi is “1” in Japanese.
41 FORGE craftsmanship
Original Products
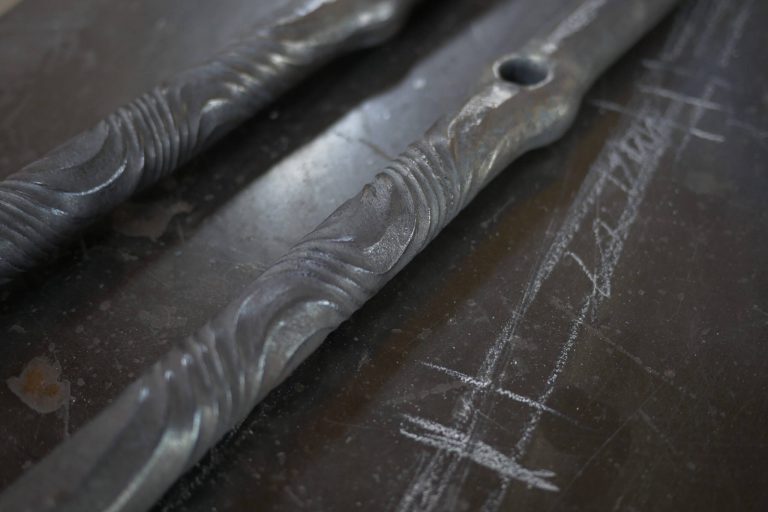
When the iron is struck while in the fire, an impression is made by overlapping hammer marks (striking marks). Taking advantage of the particular quality of iron, which is its strength and its flexibility, we create a work by hand with the greatest care. No two products are the same.
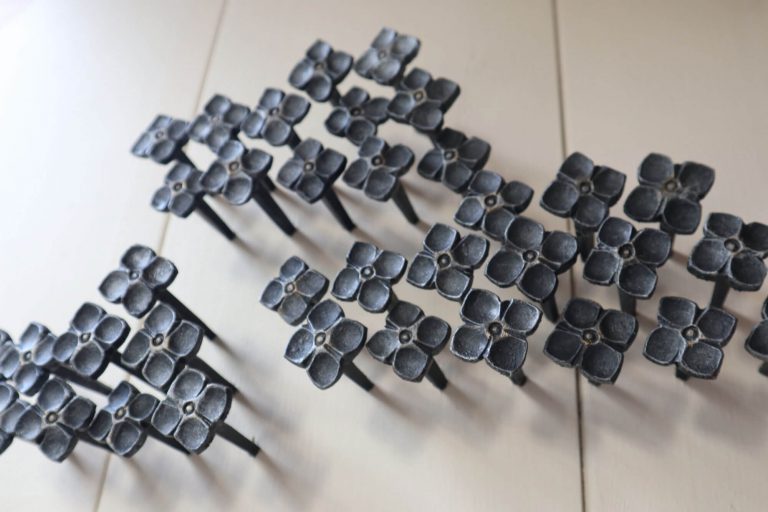
41 FORGE craftsmanship
Bringing out the best of
“wrought iron character”
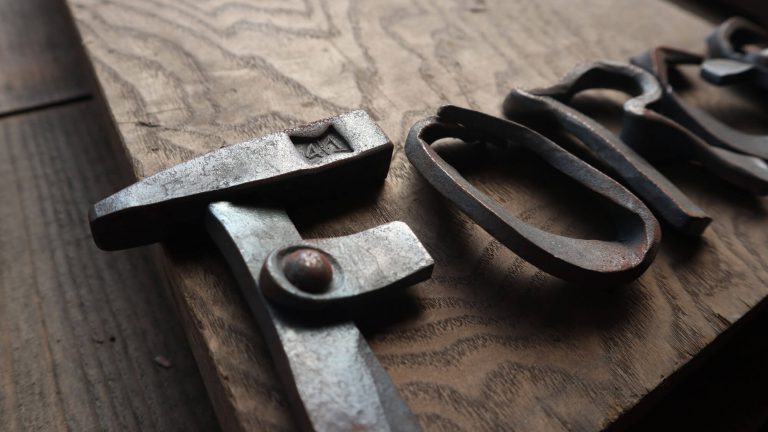
In the process of forging iron, heated iron is beaten, stretched, and bent to form shapes. “41 FORGE” pays particular attention in bringing these parts together. After the iron is ripped, it is threaded and tightened, rivetted or banded, along with other traditional techniques, to bring out the best in the solid iron.
Guided by the spirit of iron craftsmen, who took the time to create “good products,” we pursue “craftsmanship” in the modern age.
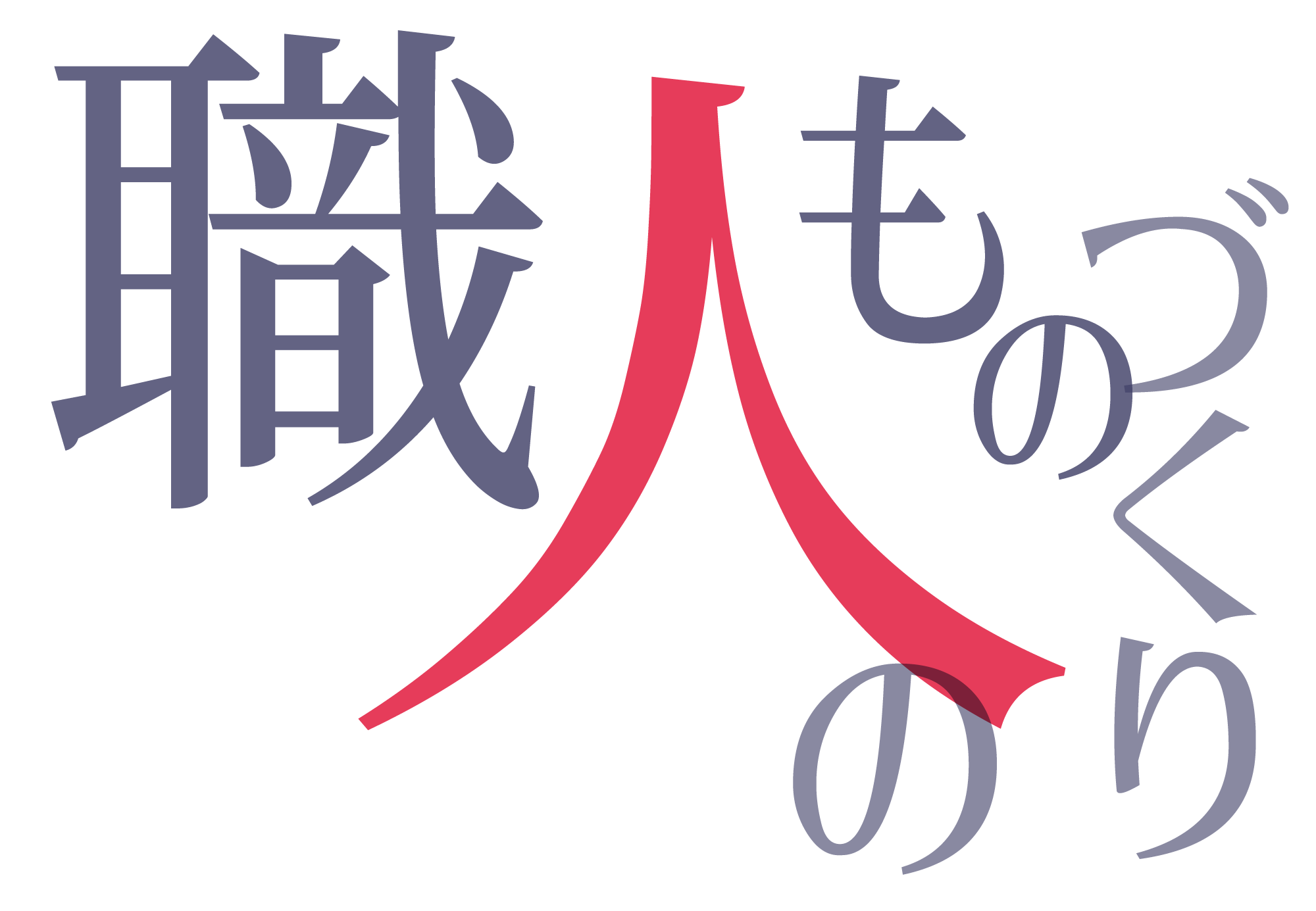
41 FORGE craftsmanship
The “user” and the “creator” work together
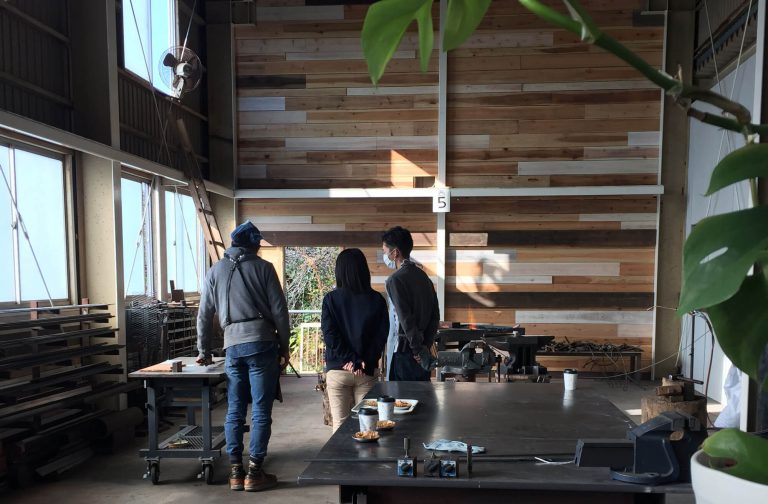
We highly prize having a good relationship with our customers and propose original designs according to their requests. We take measurements of the building as well as the site so that our products will fit beautifully in the building and the site. We try our best to meet your time and budget.
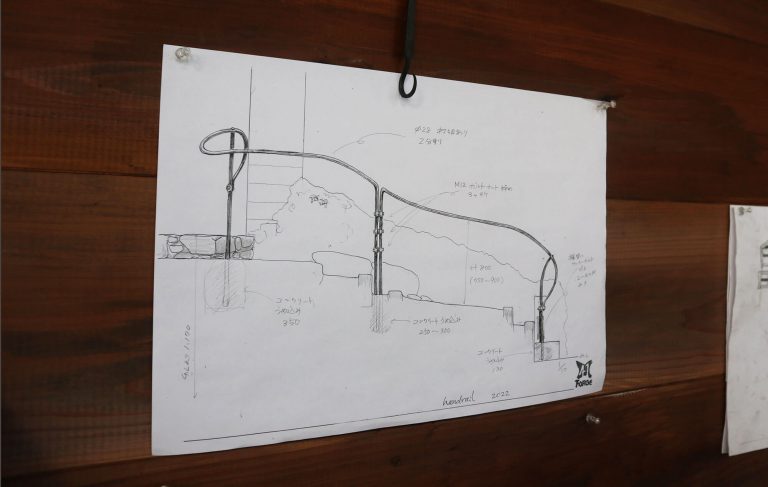
41 FORGE craftsmanship
Tool making
“for good products”
Manufacturing requires many tools. The same can be said of us. Anvils and hammers are necessary to strike iron, tongs to grip iron, vises to clamp iron, and chisels to cut, tear, and pattern iron. Various types of hammers and tongs are necessary to match the size and thickness of the material.
In European workshops, hammers alone come in dozens of shapes and sizes: large hammers are necessary for large pieces, tiny ones to do minute works. What’s more, you see a variety of other tools. The floor, walls, and shelves of the workshops are crammed with tools that have been passed down for generations and new ones made by the artists themselves.
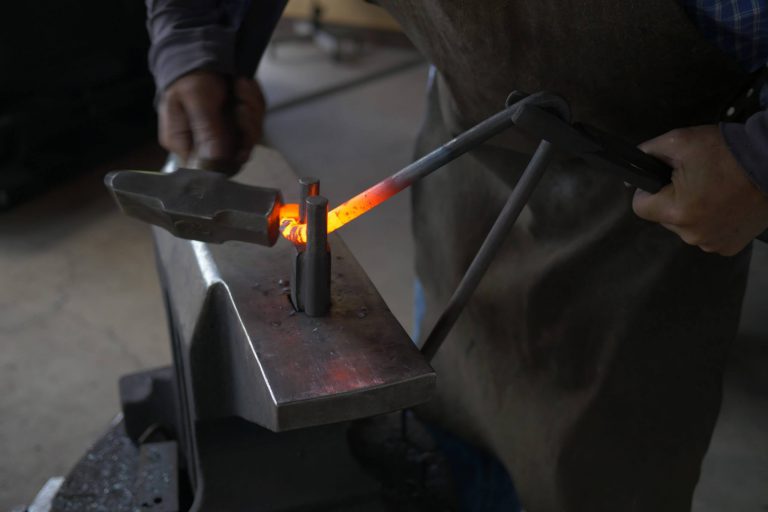
In Japan we hardly have any history of wrought iron forging, and there are no stores specializing in tools for blacksmiths.We must either use traditional Japanese forging tools, such as blade forging, or import them from Europe/US, or make them ourselves.
41 FORGE craftsmanship
Cherished for a long time
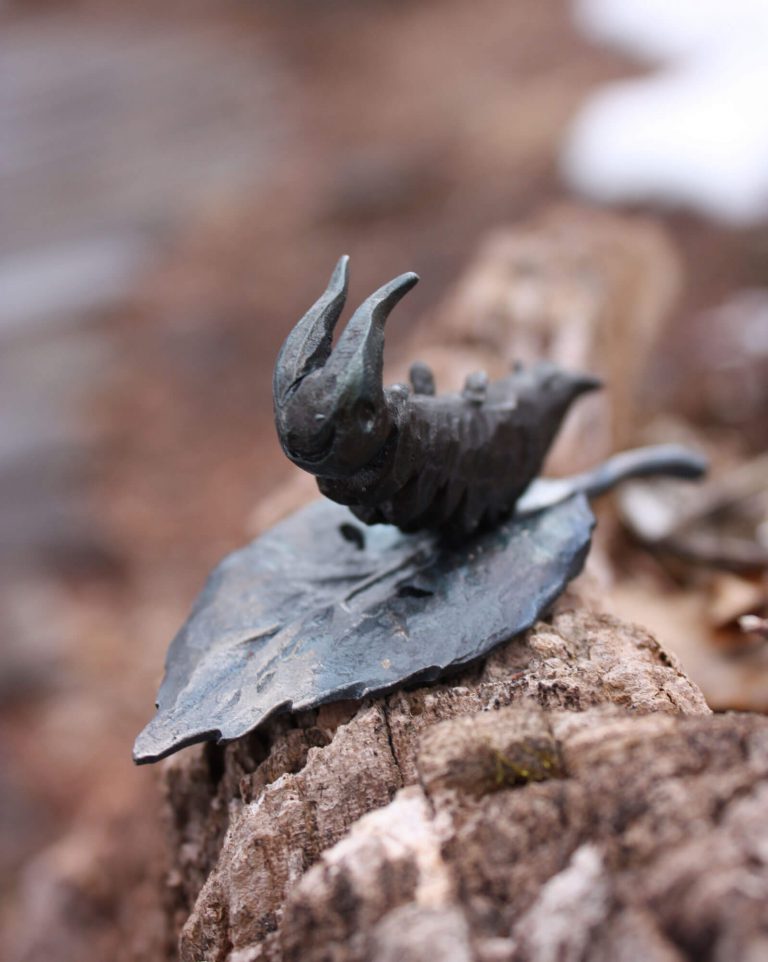
Amidst the easily and mechanically made mass products, we aim to create iron products with love and care that will be used for a long time.
At one workshop in Germany we visited, we saw a church fence being restored. We observed that the original pieces could be used for generations if they are repaired.
We hope that our products will be used for a long time, enjoyed not only for their functionality but also their strength, texture, and beauty.